There are a number of common lift problems that all property managers should be aware of – homeowners too, should you have a domestic lift installed. In this blog, we’ll be taking you through exactly what to look out for to keep lift issues at bay – plus what measures to take in the event of a technical fault.
As lifts are complex systems, they require regular maintenance to keep things running smoothly. The various components that make up an elevator system – and need routine maintenance – include:
- The lift’s cabin (otherwise known as the lift’s ‘car’)
- Cables
- Pulleys
- Motion detectors
- Air traps
If any of these components do start failing, there could be major repercussions for users of the building. In a commercial context, the likes of office workers and hotel guests can hugely rely on the continued reliability of lifts, as can firefighters in the case of fire/evacuation lifts.
If a lift of yours does start malfunctioning, you want to get it back up and running as soon as possible to help minimise disruption to your business or home life. Looking at the most common lift problems then, let’s discuss your next steps should a fault occur.
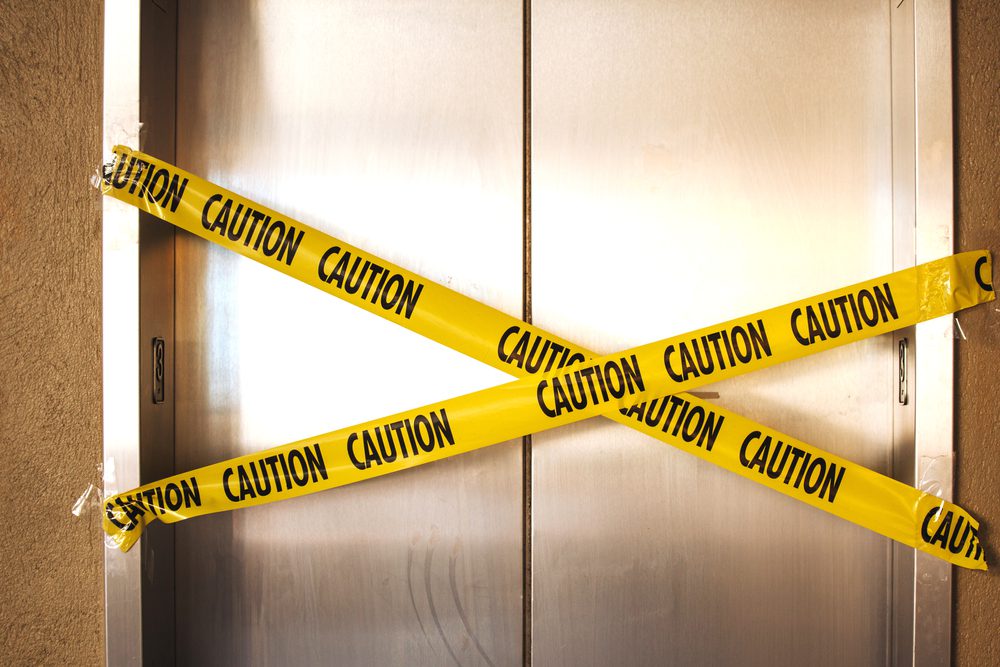
What to Do If Your Lift Has a Problem
Before we begin – it’s important that we stress here that attempting to fix a technical fault in a lift without the presence of a qualified engineer is not advised. If the issue is affecting your lift’s functionality (rather than simply its appearance), this escalates the problem to being specialist and, for your own safety, you should get in touch with a lift engineer.
What you should do to safeguard any passengers in the event of a lift problem:
- Stay calm – It’s easy to become panicked if a lift stops functioning. Panicking makes it difficult to stay in the right frame of mind to make sensible decisions. Take a few moments to settle yourself before approaching the situation.
- Communicate with the lift passengers – You can put them at ease by letting them know what you are doing to get the lift working again.
- Resist taking it upon yourself to repair the lift – This bears repeating because, if you don’t have specialist lift knowledge, you risk worsening the issue and could be putting the passengers in great danger.
- Immediately contact an emergency provider of elevator repair services – A lift technician will treat an entrapment as priority and should attend the site without delay. At Sheridan Lifts, we’ll have an engineer with you within 1 hour.
- Investigate whether you need to call emergency services – If someone inside the lift is injured, you should also communicate with them as best you can to figure out whether additional support – such as a paramedic – should be called in.
It goes without saying that the way you should respond to a lift problem will be driven by the nature of it. We at Sheridan Lifts have qualified engineers who are skilled in servicing lifts and diagnosing a wide range of lift problems.
Experiencing a problem with your lift or due a service? As the UK’s leading independent lift company with engineers stationed in all major cities, you can rest assured that help is just around the corner with us.
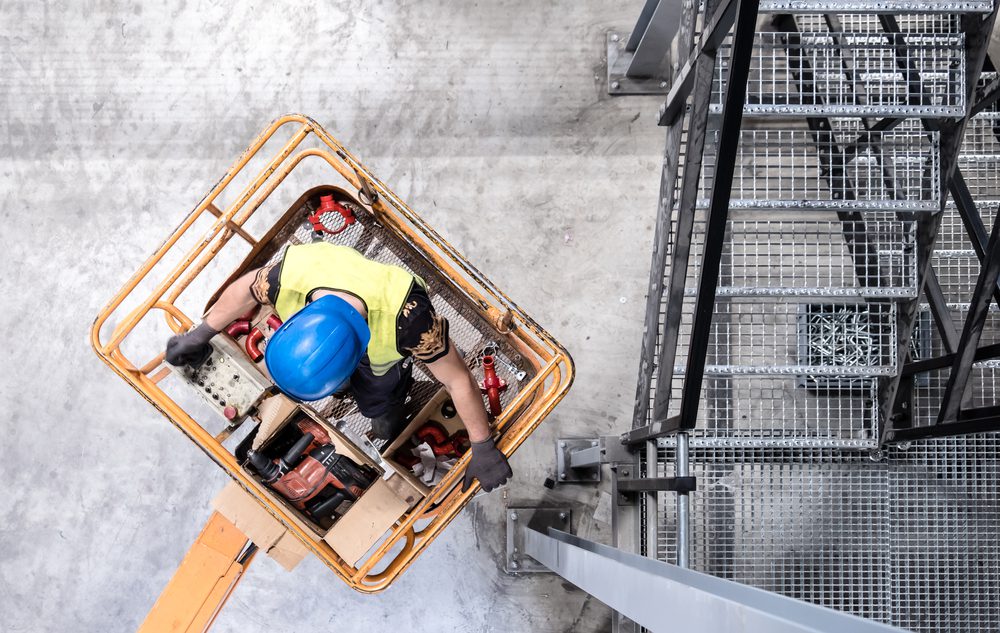
Common Problems with Lifts
Keeping a lift in good working order is a lot like looking after your personal health; as long as you work hard to continuously maintain it as well as quickly jump on problems as they start to emerge, everything will likely work without a hitch.
The analogy is also relevant in the sense that, even if you seem to be already following maintenance good practice, you should guard fiercely against complacency setting in.
Thankfully, given how often lifts tend to be used on a day-to-day basis, there are many opportunities to check how your own lift appears to be faring. The phrase ‘appears to be’ is crucial here, as you might lack the specialist expertise to diagnose many common lift problems for definite.
What you should check:
- The display that shows the next floor
- The control panel, including buttons
- Any handrails, if the lift has them
- Any other fittings inside the lift car
- The lift lighting isn’t flickering
- The gap between the lift and each floor it stops at
Of course, there’s only so much you can judge about a lift from just its outer casing. However, what you do see on it could give away problems lying in the elevator’s mechanical elements, like motors, brakes, drivers and cables – any of which we can refurbish to extend their longevity.
Here are summaries of numerous common lift problems as well as potential indicators of them…
Lift Cabin Wear and Tear
It is inevitable that various aspects of the lift cabin will decline in condition over time – since, of course, every single use of a lift contributes to its wear. A lift cabin can have many different features, such as those listed below, that are vulnerable to gradual deterioration:
- Lighting
- Control panel
- Mirrors
- Handrails
- Flooring
- Doors
Lift cabin wear and tear can start to make itself known in various ways. For example, it could begin taking longer than usual for certain buttons to trigger a response when pressed while the lift doors might not close quite as quickly as they once did.
These might admittedly come across as minor issues. However, if you notice them initially emerging towards the end of the lift’s working life, which could be somewhere between 15 and 25 years, you should see this situation as your cue to get the lift refurbished or even replaced altogether.
Paying attention to age-related wear is important because, if left unchecked, it could mean potentially disastrous consequences.
For example, the sensors, which are built into many modern lifts and intended to detect obstacles getting in the way of closing doors, can slowly become more blunt in effectiveness. Someone who inadvertently blocks the doors’ path in this case could risk suffering a serious injury or even death.
Power Supply Issues
A power failure can be one of the most common culprits for an elevator malfunctioning.
There are many different things that can trigger power failures. The most common culprits being:
- Maintenance work that hampers the overall electrical supply to the building
- A sudden storm that cuts off power to the wider geographic area
- A simple power cut, like the kind that can happen in a domestic property
- A broken fuse
Usually, though, when a power cut does reach a lift, typically the lift will react like any other electrical appliance – simply powering out. Once the electrical issue is resolved and the electric is back on, the lift will likely revert back to normal working order.
If people are caught in the lift during the outage, unfortunately the electric control system will likely be affected. As a consequence, any passengers in the lift will be unable to use it to alert people outside the lift to the situation and request assistance.
Being left in the lurch like this can undoubtedly add to the worry of being trapped. To reduce the chances of this occurring, it’s a good idea to install a backup communication system run with battery power – battery-powered backup systems will continue to work even when the power supply primarily used for your building is unavailable.
Motor Operations and Bearings
If you have noticed the lift jerking or shaking as it moves from floor to floor, physical components within the lift’s mechanism might have fallen out of alignment. This could have happened to the motor drive due to repeated use, meaning that the lift now unexpectedly accelerates or decelerates.
One distinct possibility is that the lift’s motor bearings have rolled loose and inflicted more friction to the motor. The overall lift system would therefore have come under strain, resulting in the lift cabin moving less steadily than usual in the journey between floors.
A grinding or screeching sound as the lift moves can be another sign that a bearing is malfunctioning. Leaving this problem unaddressed for too long can lead to motor failure – and it might prove cost effective to replace a lift that has a long history of motor failures.
Shaft Alignment and Key Components
When a lift stops at a particular floor of the building, this floor should be level with that of the lift cabin. Otherwise, passengers with impaired mobility could struggle when entering or leaving that cabin. Accidents can even result due to this situation.
You can, however, call lift engineers out from Sheridan Lifts – ideally before any of those accidents are given much chance to happen. We’ll carry out an inspection to check none of the following are causing the lift misalignment:
- A worn control panel
- A history of carrying excess loads
- Lost pressure (if the lift is a hydraulic model)
- Poor braking capacity
It’s easy not to initially realise when a lift is ‘mid-levelling’ – a term used for when a lift stops but slightly above or below the floor’s level. After all, this problem can start to develop over some length of time, and so the visual effect can be subtle at first.
However, if you fail to act on the problem as soon as possible, these gaps can get increasingly larger. This can make people likelier to trip or fall as they enter or leave the lift – especially given that they could so largely absentmindedly, without paying much conscious attention to the floor.
Mid-levelling can happen as a result of the lift’s brakes becoming more and more worn over time. However, a trained professional from our team can repair those brakes as well as assess the lift’s wider condition for signs of other issues with the unit’s functionality.
Strange Noises and Premature Wear
As lifts are actually designed to run in a way that makes little – if any – sound, you would have good reason to be concerned if your lift starts making strange noises when in operation.
Of course, some sounds – such as chirping noises – are so subtle that you could be tempted to just ignore them, at least for the time being. However, you need to keep in mind that, when a lift makes unusual noise, it can often be due to some major issue affecting the elevator’s mechanical structure.
For this reason, if the lift does start emitting suspect noise, you should contact a lift specialist as soon as possible to assess. It is recommended that you get in touch with this professional if the lift starts making any of the following noises you can’t explain:
- Screeching sounds
- Squeaking noises
- Clanking sounds
- Chirping noises
- Electrical noise, such as beeping noises
Any noise left uninvestigated could escalate, leaving you with not only a malfunctioning or completely out-of-action lift but also a larger repair bill than you would have had if you arranged for the problem to be sorted out earlier.
It is a common problem for lifts to make loud clunking or squealing noises – and, if this happens to your lift, it is a sign that at least one of its components has loosened or worn out.
These unpleasant sounds can potentially arise from one of the lift’s motor bearings malfunctioning – a dilemma we have already touched upon in greater detail above.
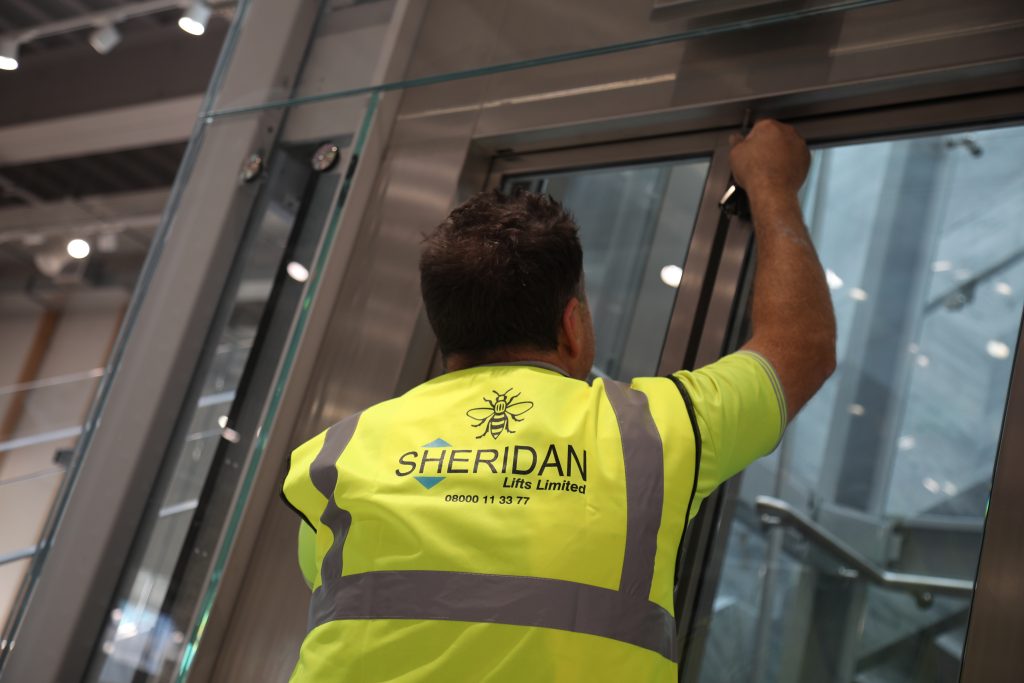
Solutions to Lift Problems
As we have noted earlier in this article, any problem with your lift’s functionality should be resolved by a lift professional. Attempting the repair yourself could lead to further damage being caused or even injury.
When it comes to lift problems, prevention is better than cure. You should therefore think meticulously about how to have a lift fitted out. You want to ensure that, if it does malfunction, anyone inside it can quickly use in-cabin systems (an emergency call button, for example) to respond to the situation.
Rest assured that, if you arrange for Sheridan Lifts to install an elevator at a commercial or apartment building, we can add all the following safety features to that lift:
- Emergency lighting – This can be installed inside the elevator compartment but connected to backup power supplies rather than the main power supply for the building. That way, even in the event of a power cut, the lift cabin can remain illuminated for the passengers’ comfort.
- A suitable communications system – The ‘suitable’ part of the equation will enable passengers trapped in the lift to use this system for getting in touch with you and letting you know that they need emergency assistance.
- Lift breakdown signage – If a lift starts malfunctioning or breaks down when people are in it, how will they know what to do? In advance, you can have signage put up displaying instructions inside the lift cabin so that these passengers won’t have to look far for guidance.
Now, what should you do if your lift is acting faulty but you can’t figure out why? Let’s explore getting to the root of the issue.
Identifying the Source of the Problem
In this article, we have already outlined a few starter tips on how to identify a number of common lift problems. However, one of many reasons why we warn you against attempting to personally fix any particular lift problem is that you might not be able to reliably discern the underlying cause.
This underlines how important it is that you ensure your lift is maintained and serviced as and when necessary. Here, it would be useful for you to establish what distinguishes lift maintenance from lift servicing. At Sheridan Lifts, we offer both of these lift solutions:
- Lift maintenance is undertaken by our skilled engineers through regularly scheduled visits. The idea here is that the lift’s mechanical components are regularly assessed so that any major defects in them can be identified before being checked again later down the line.
- Lift servicing slightly differs in not being regularly scheduled. Instead, it is organised and carried out in an ‘as and when’ fashion, in response to potential issues emerging. With lift servicing, we can inspect the lift as well as repair it during the same service visit.
Through having a lift problem identified and rectified as it is initially emerging rather than once it has firmly established itself, you can prevent it from reaching that point and consequently lumbering you with a larger repair bill than what would otherwise have been the case.
Regular Lift Inspection
You shouldn’t just schedule the occasional service for your lift. That’s because having a lift maintained and serviced more often than this can prove excellent at keeping it running safely and smoothly.
This is no small benefit – as, without it, your lift could too often be left out of action as result of time-consuming breakdowns. Imagine how much money this situation could cost a business if the lift is on its corporate premises and normally used by many visiting customers or clients.
You also need to keep in mind the Lifting Operations and Lifting Equipment Regulations (LOLER). This piece of legislation requires lift owners in the UK to:
- Have a qualified person regularly and thoroughly inspect lifts used for work activities
- Act on any findings that result from these inspections
- Ensure that these lifts can be safely used for transporting goods and people
If having to make sure your lifts stay compliant with these regulations looks like a daunting prospect, take heart that you can make the task a lot easier with one of the lift maintenance packages. We can even provide clients with bespoke service contracts for their lifts.
Our lift maintenance packages:
- Sheridan Standard – This entry-level package is ideal if, say, you need coverage for only one or two lifts, or the usage rates of the lifts you have on-site aren’t particularly high. This package offers everything you need for ensuring your lifts’ legal compliance.
- Sheridan Comprehensive – This lift maintenance package gives you everything included in the Standard package, plus 6 or 12 service visits per year and coverage for replacement parts of up to £350 per visit.
- Sheridan Premium – With this package, you are covered for not only the same service visits as previous plans but also, at no extra cost, lift breakdown repair services undertaken during normal hours – when footfall peaks and your lift’s performance is especially crucial.
How often does a lift legally need to be inspected?
If it carries people, at least every six months. If it only carries goods, at least every 12 months. The above packages make it easy for our clients to follow the well-advised route of having their lifts checked more often than the legal bare minimum.
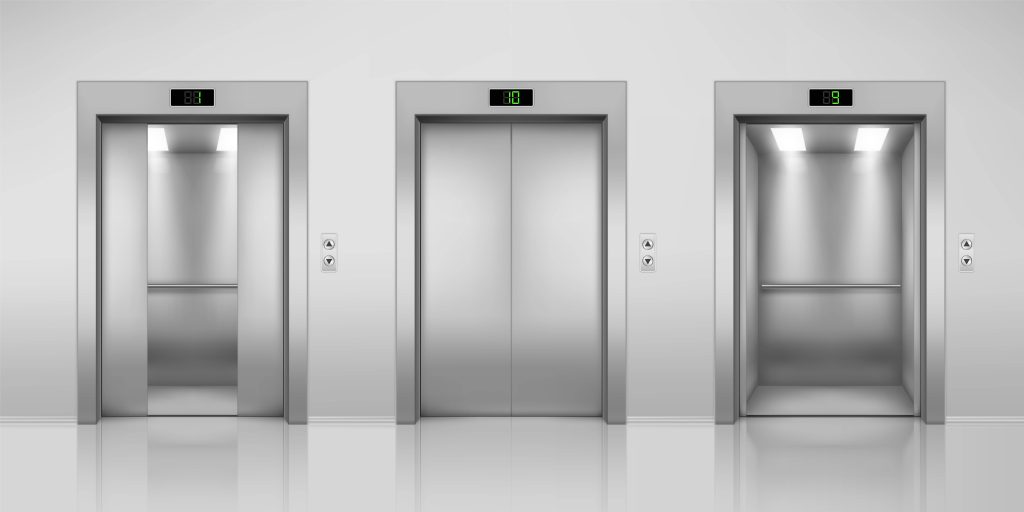
How Sheridan Lifts Can Help to Resolve Common Lift Problems
We are committed to helping our clients in not only resolving common lift problems as they arise but also proactively preventing them as much as possible.
For a start, we install lifts by assembling them from ‘open protocol’ parts. That way, if any of these parts become faulty, they can be swiftly and seamlessly replaced.
However, for existing lifts – no matter how they were originally put together and put into place – Sheridan Lifts is happy to offer long-term maintenance and repair contracts.
Got a problem with your lift and need to speak to a qualified lift technician? Let’s talk.